How you get a quality certification in 6 steps
Learn the 6 basic steps of achieving a quality or environmental certification.
Claes-Goran Hammar
10/12/20222 min read
Quality certifications are a way for professionals and organizations to verify their skills and knowledge. They can make them more attractive to customers as well as show their commitment to the industry. It also could be a requirement to pass a procurement.
Quality certifications are important because they allow professionals and organisations to prove themselves and show their customers that they are interested in providing highest quality in their field.
Step 1 - Main areas
In order to get a quality certification, you first need to work through all the business main activities. Simply, you could divide them into:
Management
Marketing
Operations
HR
Finance
These areas are seen as the business's main operation areas.
Step 2 - Processes documentation
Thereafter you need to analyze and document all the main processes within all areas, for example, in HR you have:
Recruitment
Hiring
Staff care
Ending employment
The process document within each area should show step by step for example how a recruitment is done.
All processes are sorted under each main area.
Step 3 - Set documentations
Each process now should have attached required documents, files, systems or other solution that will maintain high quality! Here you could use most of your existing documents and syste4ms etc, but some might be required to be updated and some created new to ensure there is a document or system etc for each step of the process.
The documents/systems are marked individually to be easy to find and update under each process.
A very good piece of advice is here to involve staff in the documentation, since they know their operations the best, otherwise a new and bad document/system, could cause unnecessary issues and costs.
Step 4 - Review all processes and documentation
Could you make an overall review of all processes and documentation so that all are included and that it works in real?
Suppose you have chosen to create your own quality system and would like a certification. In that case, this is normally where an external auditor would check your quality system, by reviewing all the processes and documentation.
Step 5 - Get certified
When you have made all provious steps and had a external auditor verifying in step 4, you are normally approved for quality certification.
Step 6 - Yearly review and updates
The most important step is to maintain and continuously improve the quality system by visiting the various business areas and checking how the individual processes and documentation work and improving accordingly. By doing this, you are ensuring the best possible quality that will give satisfied customers, increased sales and profits!
If you need assistance or advice in how to get your quality certification, please contact us!
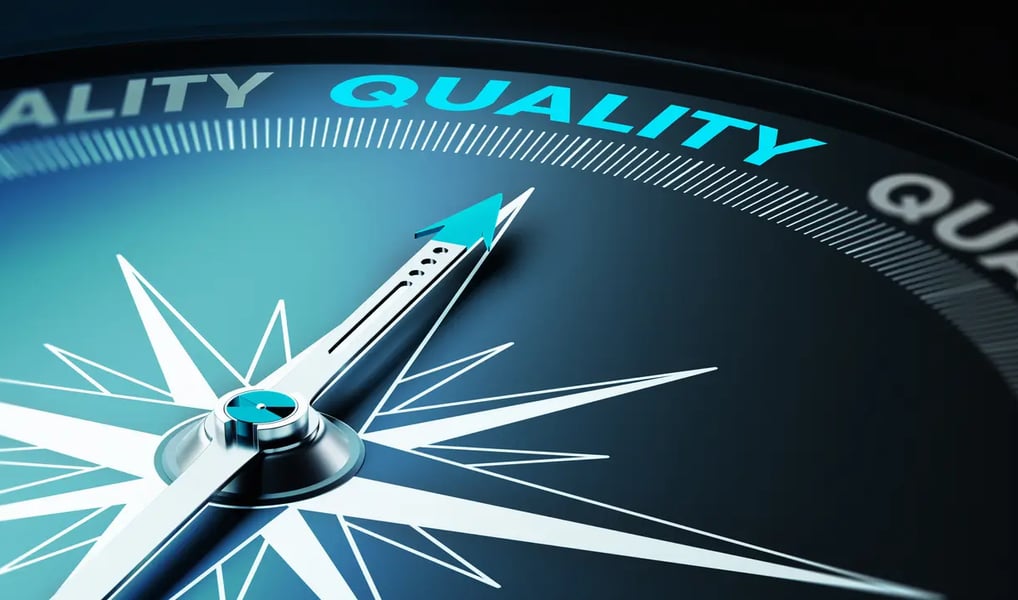
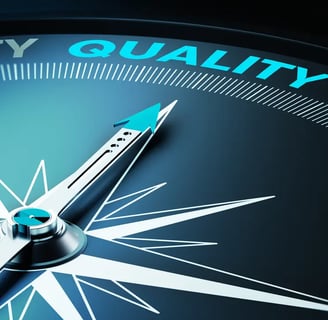
Address
QCERT, c/o: International Innovators LLC, 2093 Philadelphia Pike #6625, Claymont, DE 19703, USA
Contact
+1 (302) 213 36 03
info@qcertonline.com
About
QCERT is a smart, affordable, and “light version” of ISO9001 quality and ISO14001 environmental certification processes especially developed for startups and service SME´s that require the quality and environmental benefits, but don´t need the full work and costs of ISO9001 and ISO14001.
Copyright 2024 © QCERTONLINE