The Ultimate Guide to Quality Certification: Benefits and Processes
Get a simple overview guide on how to get your quality certification.
Claes-Goran Hammar
2/8/20234 min read
The Ultimate Guide to Quality Certification: Benefits and Processes
Understanding Quality Certification
Quality certification serves as a formal acknowledgment that an organization's products, services, or processes conform to specific standards of quality. For small and medium-sized businesses (SMBs), attaining quality certification not only enhances credibility but also provides a competitive edge in the market. It involves a thorough assessment and validation by an independent certifying body, ensuring that the company meets predefined quality benchmarks.
Among the various types of quality certifications, ISO 9001 is perhaps the most well-known. ISO 9001 is an internationally recognized standard for quality management systems (QMS). It emphasizes customer satisfaction, continual improvement, and the consistent delivery of quality products and services. Businesses across sectors adopt ISO 9001 to streamline their processes, enhance efficiency, and foster a culture of quality.
Six Sigma, another prominent quality certification, focuses on reducing defects and variability in processes through data-driven methodologies. Originating from the manufacturing industry, Six Sigma has expanded its applicability to various sectors including healthcare, finance, and logistics. By employing Six Sigma techniques, businesses can achieve near-perfection in process execution, thereby significantly improving operational performance.
In addition to ISO 9001 and Six Sigma, there are numerous industry-specific quality certifications tailored to meet the unique requirements of different sectors. For instance, the automotive industry often adheres to the IATF 16949 standard, while the food industry may follow ISO 22000 or HACCP guidelines. These certifications address industry-specific challenges and regulatory requirements, ensuring that businesses maintain high-quality standards relevant to their field.
At the core of achieving any quality certification lies a robust Quality Management System (QMS). A QMS comprises policies, procedures, and processes that collectively ensure the consistent quality of products and services. Implementing a QMS helps businesses identify areas for improvement, mitigate risks, and maintain compliance with quality standards. Ultimately, a well-designed QMS is integral to sustaining long-term quality and operational excellence.
The Benefits of Quality Certification for SMBs
Small and medium-sized businesses (SMBs) stand to gain significantly from obtaining quality certifications, both in tangible and intangible ways. One of the most immediate benefits is improved customer satisfaction. Quality certification signals to customers that a business adheres to high standards, thereby increasing trust and loyalty. Such certifications often lead to a marked improvement in product quality and service delivery, further enhancing customer experience and satisfaction.
Enhanced operational efficiency is another critical advantage. The process of obtaining a quality certification requires SMBs to streamline their operations and adhere to best practices. This often results in more efficient use of resources, reduced waste, and lower operational costs. Moreover, standardized processes facilitate smoother workflows and better communication within the organization, contributing to overall productivity.
In today's competitive market, having a quality certification can be a significant differentiator. Certified SMBs are often viewed as more reliable and professional, which can be a deciding factor for clients and partners. This enhanced reputation not only helps in retaining existing customers but also aids in attracting new ones, thereby increasing market competitiveness.
Risk management and regulatory compliance are other areas where quality certification proves beneficial. Adhering to certification standards ensures that SMBs meet industry regulations and legal requirements, thereby minimizing the risk of non-compliance penalties. It also encourages the adoption of risk management practices, helping businesses to identify and mitigate potential issues proactively.
Finally, quality certification can open doors to new markets and customer bases that prioritize certified suppliers. This can lead to higher revenue and profitability. Many large corporations and government agencies require their suppliers to be certified, providing certified SMBs with opportunities for lucrative contracts. Additionally, access to international markets becomes easier, as many countries recognize and value globally accepted certifications.
Real-world examples illustrate the tangible benefits of quality certification for SMBs. For instance, a small manufacturing company that obtained ISO 9001 certification saw a 20% increase in customer satisfaction and a 15% reduction in operational costs within a year. Another case study highlights a food processing SMB that gained access to international markets and increased its revenue by 30% post-certification. These examples underscore the potential for quality certification to drive substantial business growth and operational excellence.
Step-by-Step Process to Achieve Quality Certification
Achieving quality certification can be a transformative milestone for small and medium-sized businesses (SMBs). The journey begins with an initial assessment and planning phase. During this stage, SMBs should conduct a thorough assessment of their current processes and identify areas for improvement. Selecting the appropriate certification bodies and standards, such as ISO 9001, is crucial. This choice will depend on the specific needs and goals of the business, as well as industry requirements.
Once the planning phase is complete, the next step is to develop and document a comprehensive quality management system (QMS). This system should outline the organization's quality policies, objectives, and procedures. Detailed documentation is essential, as it provides a framework for consistent process execution and quality control. Training employees is a critical component of this phase. Ensuring that staff are well-versed in the QMS and understand their roles within it fosters a culture of quality and accountability.
Internal audits are an integral part of the implementation phase. These audits help identify potential non-conformities and areas for further improvement before the official certification audit. Regular internal audits ensure that the QMS is functioning as intended and that the organization is prepared for the external audit. Practical tips for conducting effective internal audits include establishing an audit schedule, using checklists to ensure thoroughness, and engaging employees at all levels.
During the certification audit, an external auditor will evaluate the QMS to ensure it meets the required standards. It is essential to be well-prepared and to address any non-conformities promptly. Open communication with the auditor and a willingness to make necessary adjustments can facilitate a smoother audit process. Post-certification, maintaining and continually improving the QMS is vital. Regular reviews, training updates, and staying informed about changes in standards will help SMBs sustain their certification and enhance their quality management practices.
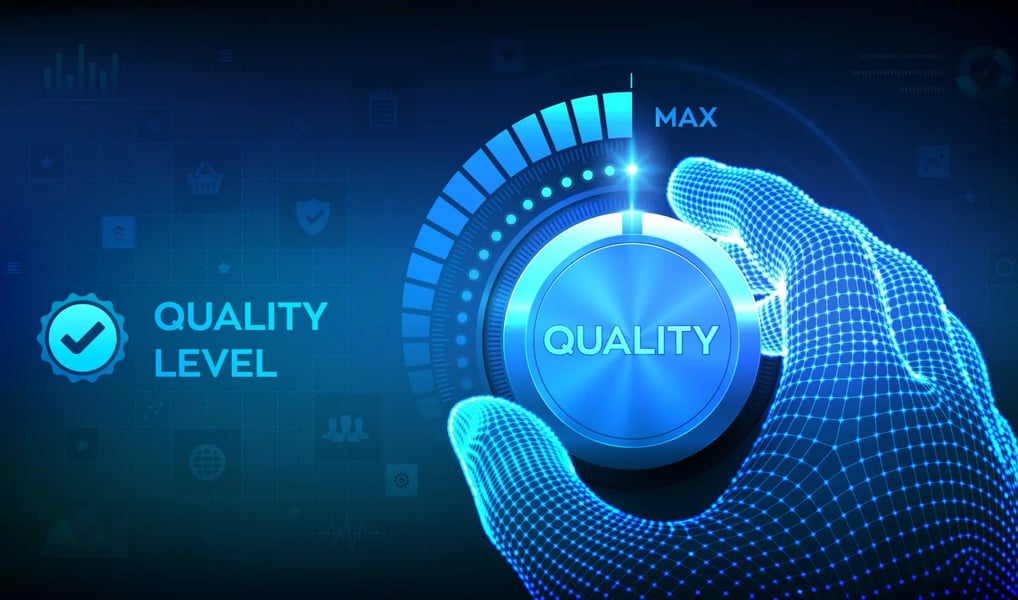
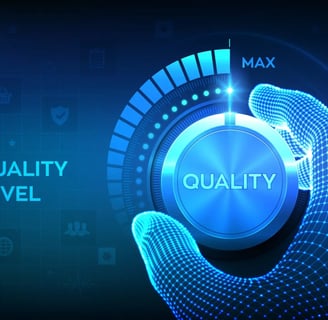
Address
QCERT, c/o: International Innovators LLC, 2093 Philadelphia Pike #6625, Claymont, DE 19703, USA
Contact
+1 (302) 213 36 03
info@qcertonline.com
About
QCERT is a smart, affordable, and “light version” of ISO9001 quality and ISO14001 environmental certification processes especially developed for startups and service SME´s that require the quality and environmental benefits, but don´t need the full work and costs of ISO9001 and ISO14001.
Copyright 2024 © QCERTONLINE